RIVERSIDE RED X – 2401 NW Platte Road, Riverside, MO 64150
Positioning Sensitive Levee Land to Relaunch an Iconic Hometown Business
If you know about the town of Riverside, Missouri, you know about the family-owned Red X on NW Platte Road. The huge grocery, liquor, and retail landmark has been a popular shopping destination for people all over the Kansas City area since the 1950s. All those years are evidence of the business’ success, and its momentum shows no signs of slowing.
Ideas for remodeling the Riverside Red X to make better use of its existing space gave way to a realization that more space was needed — a lot more. Red X owners embraced plans for building a whole new store to replace the old store right next door on land they’ve owned for years. They decided to develop about six acres to build a 59,000 square foot structure that would become the new Red X with enough room to accommodate the company’s full potential.
The build site was nothing resembling simple, straight forward farmland. It’s Riverside Quindaro Bend Levee land, substantially elevated by the Army Corps of Engineers (USACE) decades earlier. Raising the land helped fortify the levee protecting Riverside from disaster and keeps anything built on the land out of easy reach of rising waters.
The project team, led by Crossland Construction Co. Inc., brought in Alpha-Omega Geotech almost from the beginning. They’re familiar with our extensive experience drilling in delicate soils near rivers without disturbing the critical balance that holds the entire flood protection system together. Plus, we know USACE rules and requirements like the back of our hand.
“You need specific approval from the USACE and you have to coordinate with the Levee District for any development within 500 feet of the levee centerline,” says AOG Engineering Director Garic Abendroth. “In this case, the 500 foot mark was right in the middle of the build site, so we helped secure approval and cleared the way for construction.”
AOG’s long history of working in unusual and unknown subgrade conditions also made our Geotechnical skills a smart match for the project. The USACE’s original build up of the land involved undocumented fill material, making an already complicated challenge even more complex.
“Planning careful, highly-strategic drilling and engineering is just the beginning,” says Abendroth. “Ultimately, we also have to make sure our recommendations work well with the existing levee. You can’t pretend you’re just in the middle of a field. You have to know exactly what you’re dealing with, and understand how every piece of the bigger picture fits together, including USACE requirements and the owner’s budget. This is something we do well.”
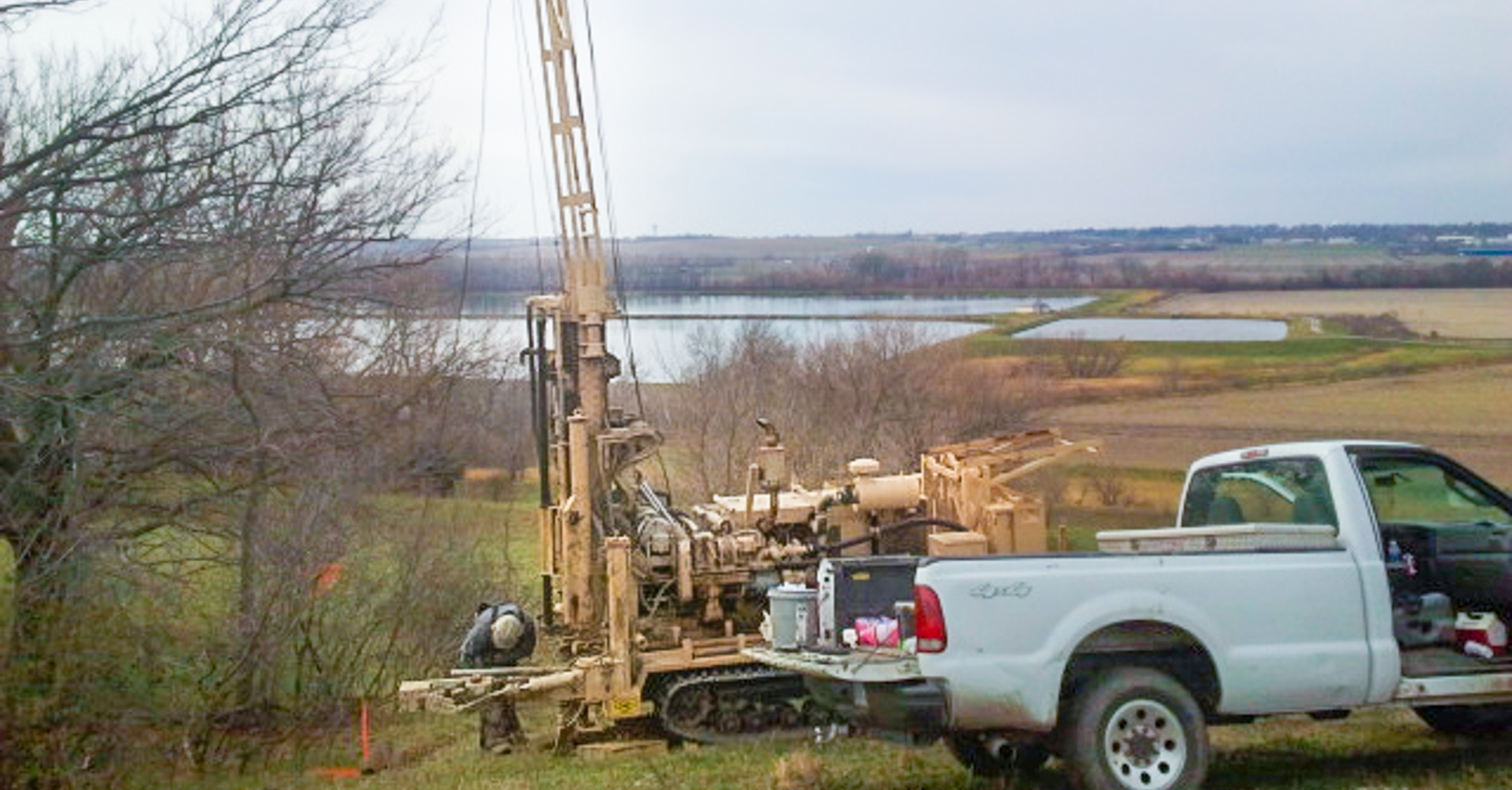
AOG has extensive experience drilling in sensitive areas and unusual conditions near bodies of water.
Pinpointing a Solution in a Rocky, Controlled Levee Area
Red X owns the land, but didn’t have much flexibility with how it could be handled. Options are limited when you’re dealing with a designated ‘controlled’ levee area that’s manmade and stretches farther from the river than the untrained eye might see.
The levee itself slopes down sharply to the more level, controlled area extending into Red X property. Deep below the surface, the USACE had created a sand layer topped with a clay cap to keep river water from bubbling up. Abendroth says the USACE then added a thick layer of uncontrolled fill material on top of the clay to strengthen the subgrade and elevate the surface. The fill was rocky, jagged, and difficult to manipulate.
“It was about 20 feet of gravel, broken limestone, and concrete chunks. Everything from a grain of sand up to pieces that were two or three feet in size. Whatever could fit into a dump truck. Back then, it all probably came from a nearby road excavation. I immediately began thinking and collaborating with the project team about foundation support options given what we had to work with.”
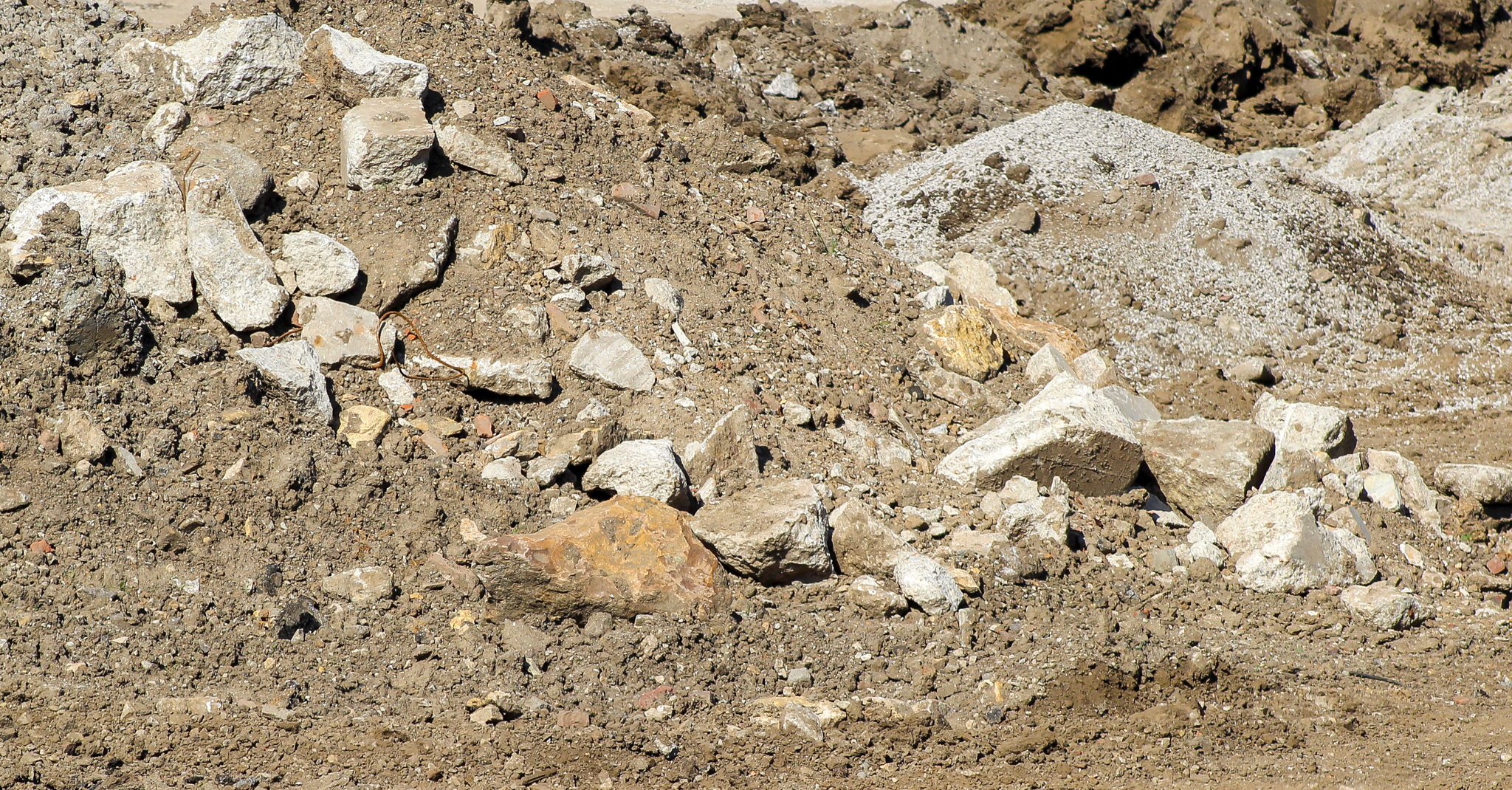
Rocky fill material used to elevate the ground decades ago.
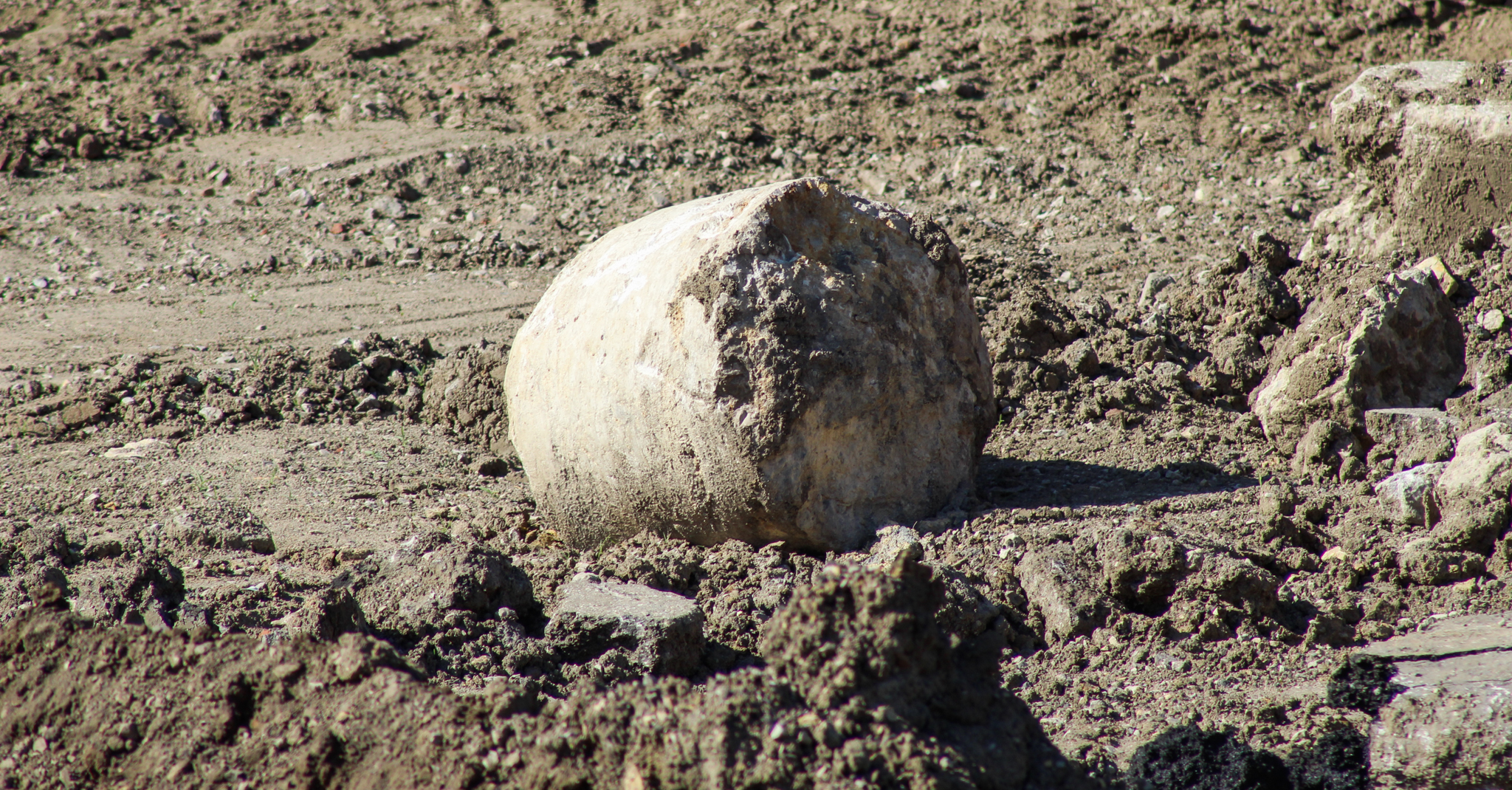
One of many large chunks posIng challenges to drills and structure support strategies.
AOG’s recommendation could have been simple, conservative, and expensive, calling for tearing all of it out, and then importing better material to replace it. However, that would have pushed the project budget too high. Ground improvement was another option. It would have involved drilling shafts filled with highly-compacted gravel to boost the overall stability of the subgrade. But drilling those shafts could get expensive quickly as your drill hits chunk after chunk of unforgiving concrete. The risk of difficult, expensive drilling to support a deep foundation all the way down to bedrock was also unappealing.
“It’s not like just drilling straight through something like clay,” says Abendroth. “You might hit bricks or blocks of limestone. You can’t know until you get into it. And when you consider that many drilling locations will be involved, costs start to shoot up.”
AOG proposed a support platform that struck a better balance in terms of project priorities, from risks to costs. It involved removing just a few feet of the uncontrolled fill at the surface and then replacing it with engineer controlled fill consisting of crushed rock wrapped in geogrid. Picture a broad meshed platform sort of resembling a burrito. It’s designed to perform much like a snowshoe, absorbing a structure’s weight load and spreading it across the crushed rock.
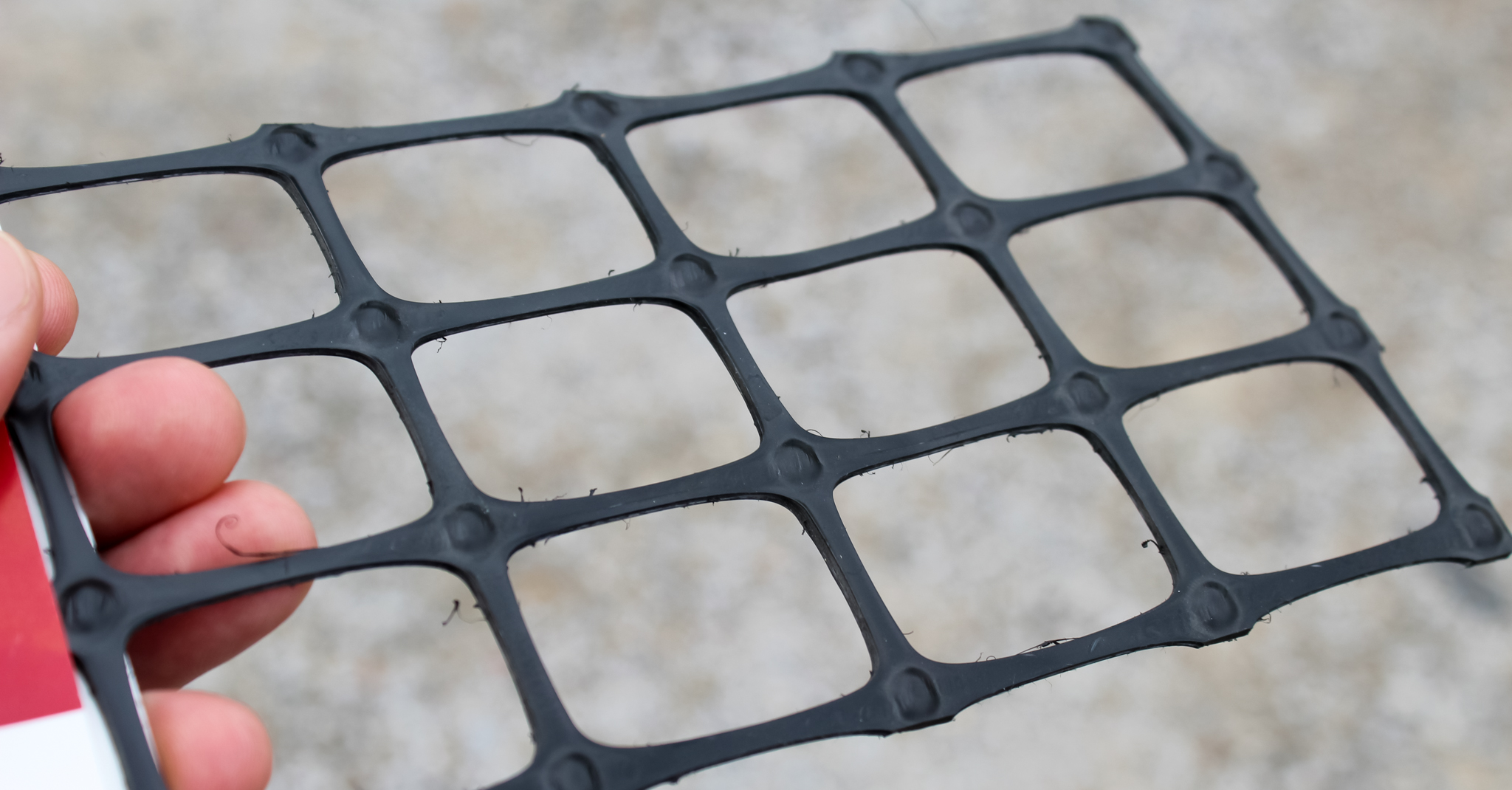
A sample of flexible geogrid used to wrap compacted crushed rock to form the platform.
Constructing the geogrid reinforced platform began with investigative borings, as deep as 90 feet in some spots, to verify the characteristics of the sand and clay at the bottom. Then crews dug out about four feet of the undocumented fill along the surface and replaced it with carefully controlled engineered material.
“Each lift that went into making the platform needed to be a very specific thickness,” explains Abendroth. “We had to document the compaction density and moisture to ensure the quality of what was put back in. We left the deeper undocumented fill in place beneath the platform because it’s been there for a half century and has certainly settled.”
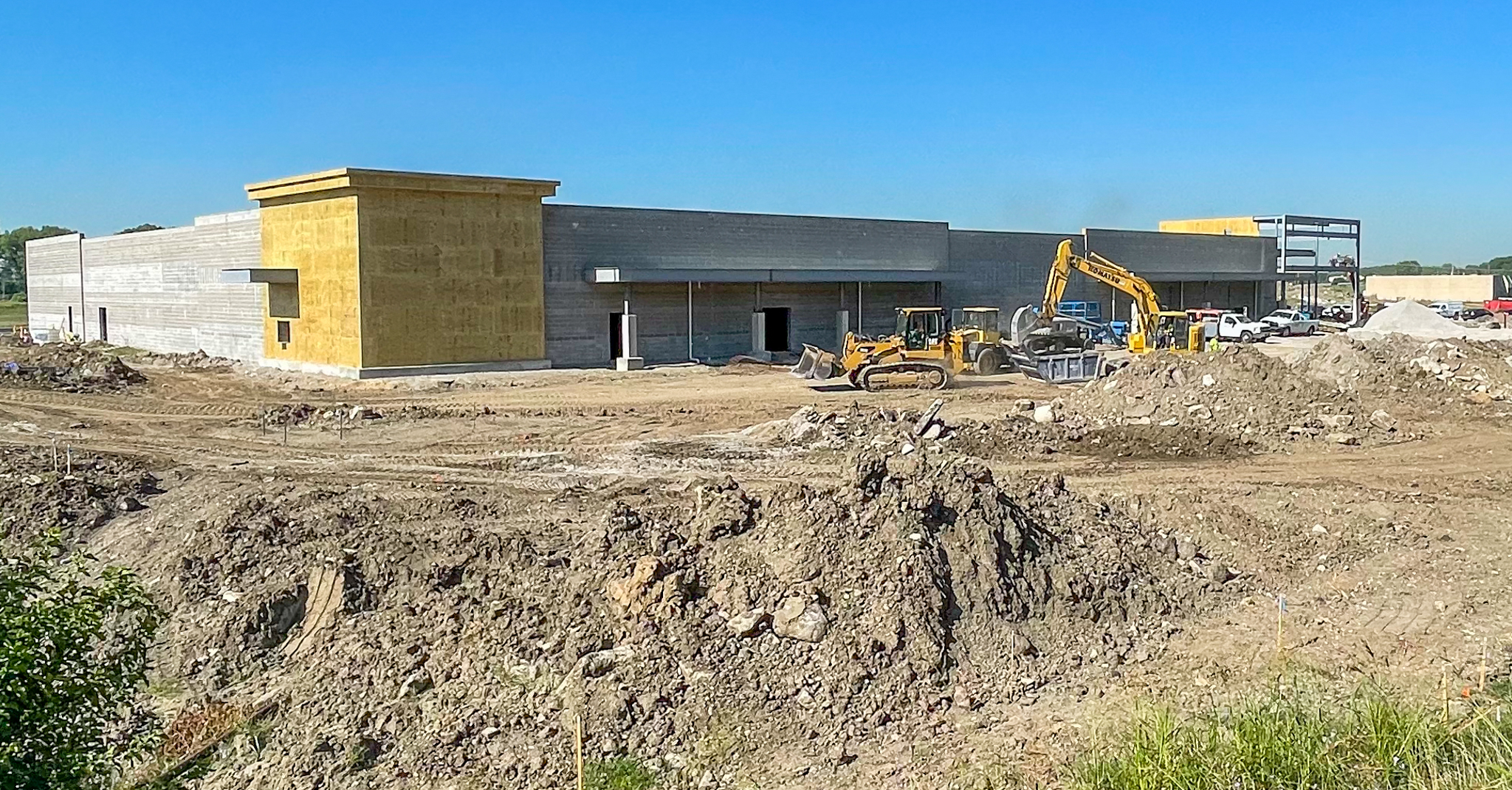
The new Red X structure is supported by a geogrid reinforced platform.
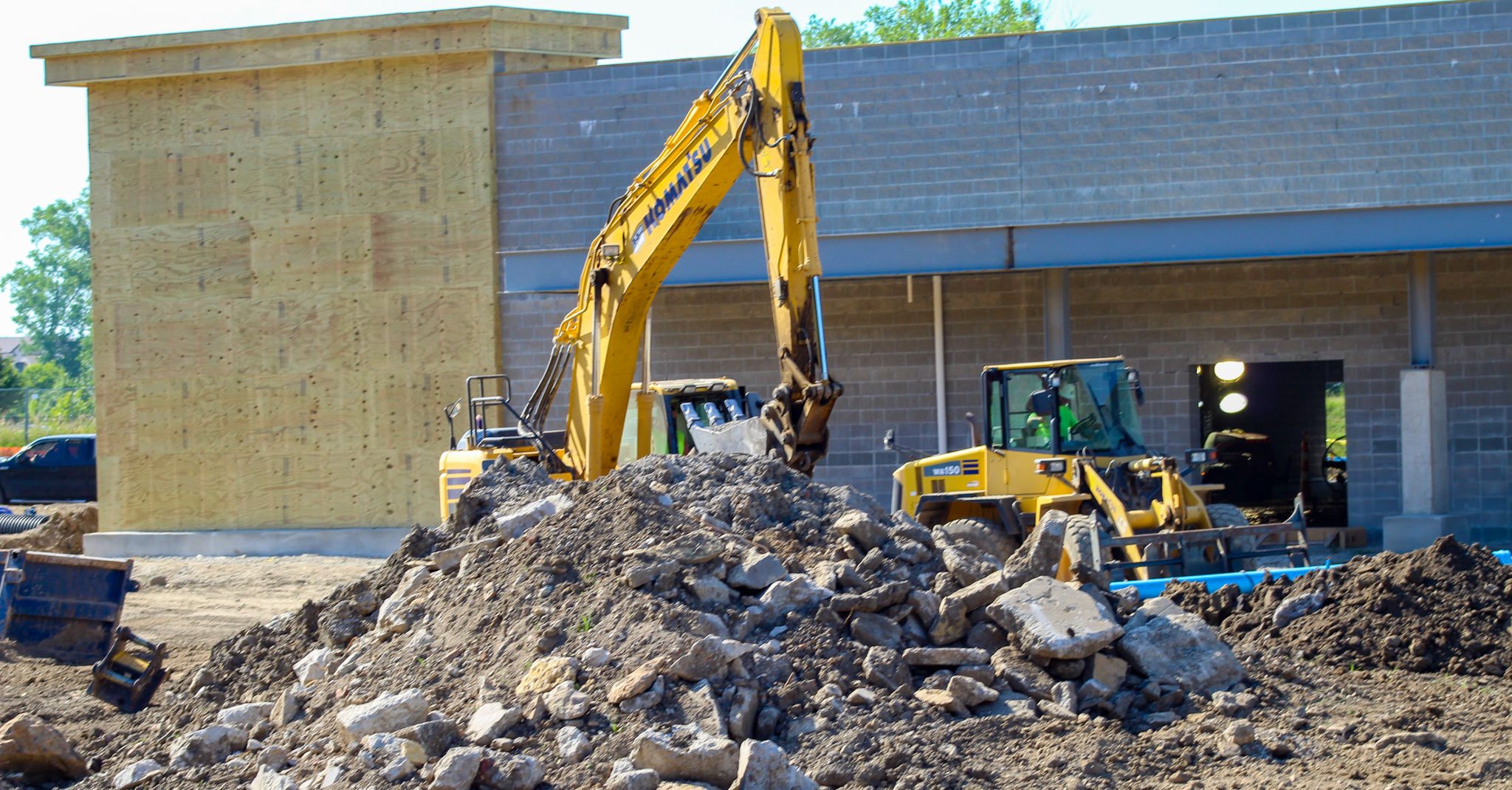
Development of a smaller version of the same platform to support the new parking lot.
The new Red X also needed a large customer parking lot. AOG engineered a smaller version of the geogrid reinforced platform to support that area too. Abendroth says creating the right conditions beneath a parking lot is harder than you might think.
“It gets very complicated and that’s when experience really serves us. When you’re dealing with sand, gravel, and clay mixed together, every spot can be different so you have to proof-roll it and visually understand what you’re seeing.”
Proof-rolling puts the parking lot platform to the test as it’s coming together. A dump truck is brought in and slowly rolled over the material while technicians watch carefully for stability issues and make adjustments. Then, gravel goes on top of the platform followed by asphalt on the surface.
“You really want to get it right because if you don’t, you’re asking for buckling or potholes long before you expect them to happen,” says Abendroth. “Those kinds of problems can force the temporary shutdown of customer parking for repairs and that’s not good for business.”
Abendorth says experienced field technicians are critical for proof-rolling, and that’s another reason AOG stands out. “Our field techs are crucial. They need a lot of experience to know what to look for and how to make adjustments. It’s not an entry level challenge. You’ve got to have people who have seen it before many times and really understand.”
AOG technicians also remained on site for Special Inspections as the new Red X structure came out of the ground and took shape. The project team opted to not split up Geotechnical Engineering and Special Inspections responsibilities because they know consistency is a valuable advantage that comes with sticking with one partner.
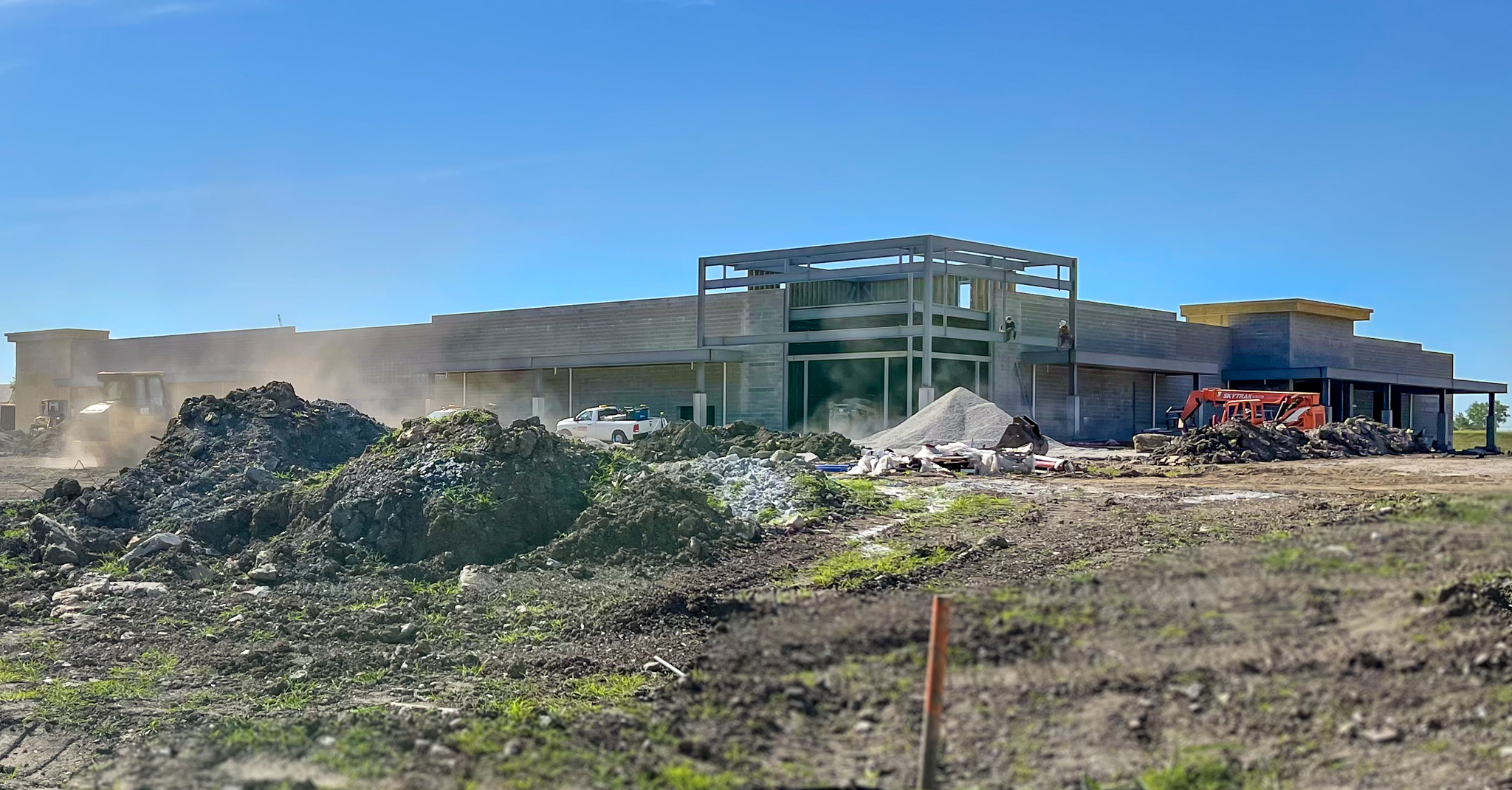
Construction of the new Riverside Red X. August, 2022.
Working Together for a Community Achievement
The new Riverside Red X is a good example of the benefits of a collaborative construction effort almost from square one. Early strategizing and planning with our AOG team streamlined everything from handling levee sensitivities and permissions to crafting a support platform in context of so much undocumented fill material. Project partners working closely together were in the best position to figure out the best solutions in consideration of available materials, USACE requirements, and rigid budgets. Working on the new Red X is the kind of challenge that brings out the best in AOG, and the kind of processes we’re known for.
“We never want to just work in isolation, do our part and go home,” says Abendroth. “We know the best results for each project come from smart minds pooling their thinking and customizing solutions exactly right for the problem. And every build site in the Kansas City area is unique.”
Project Partners:
General Contractor: Crossland Construction
Architect: BRR Architecture
Structural: Johnston Burkholder Associates
Civil: McClure Engineering Co